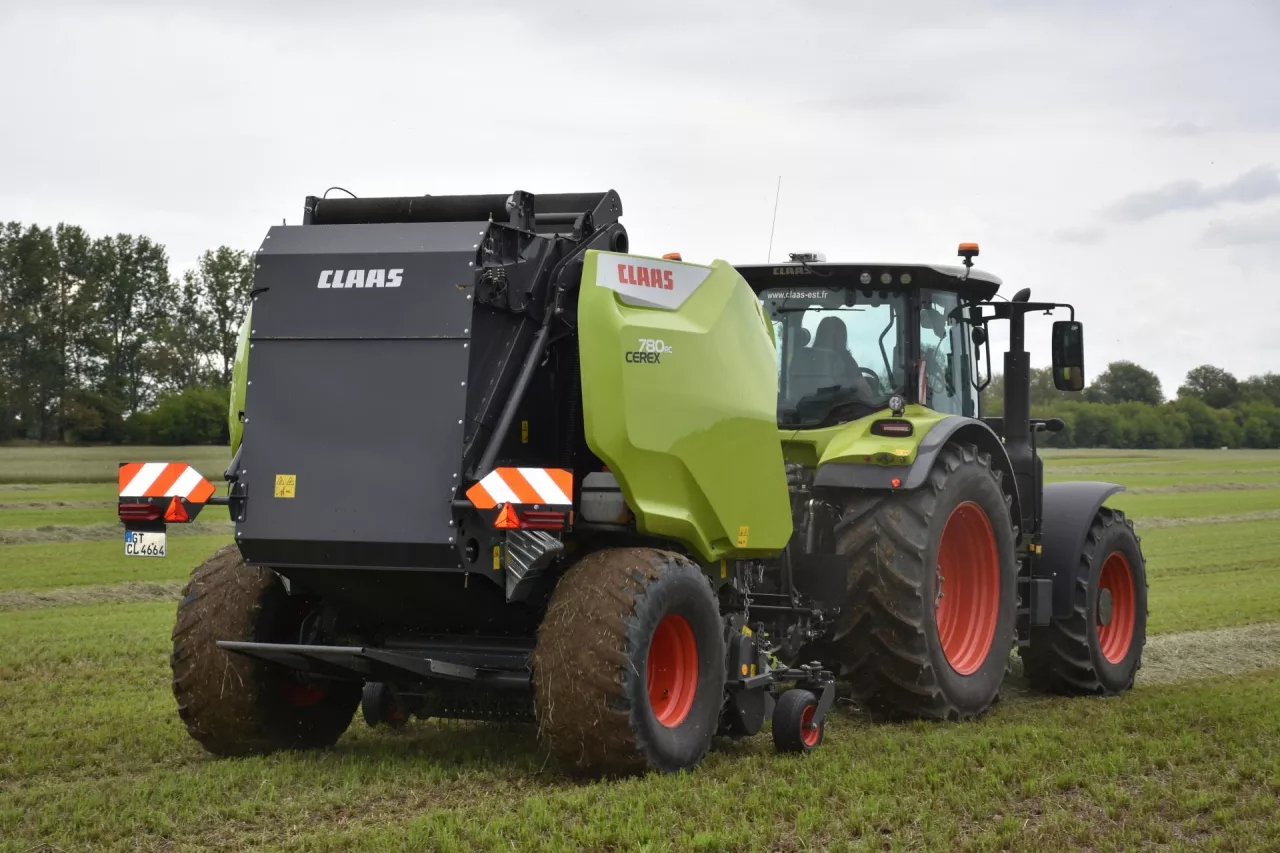
Podczas zwiedzania od razu rzucało się w oczy, to jak relatywnie niewiele osób tam pracuje. Dlaczego? Odpowiedź jest prosta, bo wiele prac wykonują roboty. Właśnie wszechobecne zautomatyzowanie robi największe wrażenie. Sprawa jest prosta, człowiek szybciej się męczy, a wtedy może się pomylić. Roboty nie znają takiego pojęcia. Ale przejdźmy do rzeczy.
Jak zaoszczędzić na paliwie?
Najbardziej zaawansowanym mechanizmem przeniesienia momentu obrotowego z silnika na koła jest bezstopniowa przekładnia CVT (continuous variable transmission). Mniej komfortowo jest podczas pracy ciągnikami z przekładniami manualnymi, bo może się zdarzyć, że pracujemy na zbyt wysokich prędkościach obrotowych silnika, co powoduje wysokie zużycie paliwa. Przekładnia CVT ma nieskończoną liczbę przełożeń dopasowując obroty silnika do obciążenia w taki sposób, aby były one jak najniższe, co zdecydowanie ogranicza spalanie. To niezwykle istotne przy galopujących cenach paliwa.
Najpierw szkice projektowe
Claas zaczął swą przygodę z przekładniami bezstopniowymi w 2007 r. Biuro konstrukcyjne i zakłady produkcyjne umieszczono w fabryce CIT (Claas Industrietechnik) w Paderborn w Nadrenii-Północnej Westfalii w Niemczech. Jednym z członków zespołu projektowego został dr inż. Timo Wendt.
– Naszym celem było stworzenie uniwersalnego mechanizmu, który będzie trwały i niezawodny. Prowadziliśmy setki dyskusji, opracowaliśmy tysiące koncepcji i szkiców, a także budowaliśmy modele i prototypy. Zajęło to kilka lat, owocując uruchomieniem produkcji seryjnej w 2014 roku. Tak narodziła się bezstopniowa przekładnia Cmatic – wspomina dr Wendt.
Testy przekładni
Gdy prototyp CVT był gotowy, inżynierowie Claasa rozpoczęli serię testów na stanowisku badawczym. Oceniano przede wszystkim współpracę części mechanicznych i hydraulicznych. Przekładnia jest skomplikowanym mechanizmem, łączącym współpracę układów klasycznych kół zębatych i sprzęgieł. Ale to nie wszystko, bo jest jeszcze zaawansowany układ hydrauliczny z zespołem dwóch jednostek hydraulicznych, które w zależności od używanego zakresu jazdy są pompą lub hydromotorem.
Dopracowany prototyp przekładni został następnie przeniesiony z laboratorium badawczego i zamontowany w ciągnikach Claas Arion serii 500 i 600. Próbne wersje przekładni Cmatic przeszły w sumie ponad 20 tys. godzin testów w różnych warunkach polowych. Traktory w nie wyposażone regularnie kontrolowano w serwisie. Analizowano pod mikroskopem niemal każdą kroplę oleju. Badania obejmowały również zmęczenie poszczególnych komponentów przekładni. Po tysiącach godzin drobiazgowych analiz i testów porównawczych można było wydać wewnętrzną opinię o nowym wynalazku marki Claas. Trwałość przekładni Cmatic oceniona bardzo wysoko.
Seryjna produkcja ruszyła w 2014 r., a do połowy 2022 r. zbudowano już ok. 10 tys. mechanizmów. Wygląda na to, że rynek je przyjął, bo popyt na CVT z Paderborn ciągle rośnie.
Jak działa przekładnia Cmatic?
Przekładnia Cmatic jest modułowa i składa się z części mechanicznej i hydraulicznej. W części mechanicznej jest podwójne sprzęgło i przekładnia planetarna. Ale uwaga, zrezygnowano dla nich z kąpieli olejowej, by ograniczyć opory ruchu w oleju. Dlatego miska olejowa jest poniżej zębatek i smarowanie odbywa się za pomocą specjalnego systemu.
Cała konstrukcja CVT ze stajni Claasa pozwala na rozdzielanie i sumowanie mocy hydraulicznej i mechanicznej. Zakres pierwszy – sprawdza się do prac z prędkością poniżej 20 km/h, a zakres drugi – włącza inne przekazanie momentu obrotowego i sprawdza się powyżej 20 km/h. Co ciekawe, moduł hydrauliczny jest zasilony tym samym olejem, który krąży w obiegu siłowym ciągnika i napędza zaczepiane maszyny. Dlaczego zdecydowano się na takie rozwiązanie, a nie na zamknięty, osobny obwód tylko dla CVT?
– Praca w jednym systemie olejowym upraszcza serwis i uzupełnianie ubytków oleju. To nasz autorski pomysł, aby bazować na jednym rodzaju oleju. Łatwiej też wtedy sprzęgać ciągnik z innym sprzętem. Ceną, jaką płaci się za takie udogodnienie, była konieczność opracowania bardzo szczegółowego zespołu filtrów, aby żadne zanieczyszczenia nie przedostały się do precyzyjnych mechanizmów Cmatic – mówi dr Timo Wendt.
Czystość i jeszcze raz czystość
Większość komponentów przekładni CVT produkowanych jest od podstaw w Paderborn. Koła zębate i wałki powstają z odlewów i odpowiednio przygotowanych elementów ze stali, skrawanych później w obrabiarkach numerycznych. Nowy element jest dokładnie myty i pakowany w foliowe torby, dla ochrony przed zabrudzeniem i korozją.
Przekładnie Cmatic składane są na linii montażowej. Jest to praca ręczna i zaczyna się od najdrobniejszych elementów, łączonych w coraz to większe zespoły. Pracownicy obsługują wydzielony odcinek linii – Na każdym stanowisku króluje wszechobecna elektronika, komputery oraz nieodzowne elektro- i pneumonarzędzia, ułatwiające montaż.
Zaczyna się od przekładni planetarnej
Powstaje ona na mobilnych stołach montażowych, które wyposażone są w specjalne otwory i plastikowe wsporniki oznaczone odpowiednimi symbolami. Są one – na początku linii – uzupełniane składowymi częściami przekładni: łożyskami, pierścieniami uszczelniającymi, kołami zębatymi, wałkami i tulejami. Ten wyliczony komplet części ułatwia zadanie montażystom; budują oni bowiem mechaniczny zespół przekładniowy z ograniczonej ilości "klocków", pasujących do siebie. Cały czas mają do pomocy elektroniczną instrukcję montażu, wyświetlaną na monitorze.
Skompletowany stół-przybornik uzupełniony przez pracownika przesuwany jest po szynach do kolejnej osoby, która zaczyna w odpowiedniej kolejności łączyć części. Po dokonaniu swej pracy, przesuwa stół do kolejnej osoby. Na każdym kolejnym stanowisku skomplikowany mechanizm rozrasta się o nowe podzespoły. W wyznaczonych miejscach na prasach wciskane są łożyska. Zmontowane przekładnie planetarne obudowywane są kolejnymi częściami. Finalnie trafiają do większych obudów-odlewów, w których będą pracować.
Profesjonalizm przy każdej śrubce
Wraz z rozrastającą się konstrukcją mechaniczną zespołu części mechanicznych i hydraulicznych, tworzących nową Cmatic, zmienia się też sposób transportu tego produktu wewnątrz fabryki. Coraz to większe komponenty przenoszone są na indywidualne wózki elektryczne, na podwoziu których odbywa się montaż kolejnych części. W końcu rdzeń CVT trafia do działu skrzyń biegów.
– Wszyscy pracownicy tego działu mają nie tylko wykształcenie techniczne, ale także odpowiedni czas pracy i staż w naszej fabryce. Tylko najbardziej wykwalifikowanym osobom w naszym zakładzie możemy powierzyć finalny montaż przekładni, która jest przykładem wspaniałej myśli inżynieryjnej. W jednej obudowie Cmatic współpracuje bowiem ze sobą ponad 700 części mechanicznych i hydraulicznych, które muszą wytrzymać ciśnienie ok. 500 barów – mówi Waldemar Kasnitz, szef Działu Product Division Terra Trac and Transmissions, Claas CIT Paderborn.
Kontrola fabryczna
Proces montażu nowa przekładnia Cmatic poddawana jest rygorom surowej kontroli fabrycznej. Monitorowane są wszystkie etapy według określonej procedury. Co ciekawe, każdy z pracowników ma za zadanie zalogować się przy pomocy swego chipu, że wykonał już przewidzianą dla jego stanowiska pracę przy przekładni.
Kontroli podlega nawet etap dokręcania śrub! Sprawdza się momenty obrotowe kluczy dynamometrycznych. Rozwiązano to w ten sposób, że w wraz ze zamianą nasadki na kluczu, zmianie ulega automatycznie siła, z jaką przykręcana jest dana śruba. Po przejściu kompletnego cyklu montażowego, na schodzącą z taśmy przekładnię czeka ostateczny test. Obejmuje on każdą skrzynię biegów Cmatic.
Ostateczne sprawdzanie
Test polega na umieszczeniu przekładni na łożu w specjalnej kabinie. Podłączane są do niej przewody olejowe i elektryczne, a także wałki zasilające i odbierające moc. Cały test kontroluje wszędobylska elektronika, która skrupulatnie skanuje wszystkie funkcje przekładni, uzyskiwane przez nią prędkości i moment obrotowy. Sprawdzana jest temperatura pracy, przepływ oleju i sprawność wszystkich czujników. A kiedy już mechanizm pozytywnie zaliczy swój "egzamin dojrzałości", dostaje zielony certyfikat i może być instalowana w ciągniku.
Zanim to jednak nastąpi, nowo narodzony Cmatic pakowany jest w szczelny plastikowy worek, chroniący przed korozją. W takiej kołderce trafia do magazynu, a następnie jedzie do Francji, do zakładu Claas w Le Mans, gdzie jest montowana do ciągników. Ale to już historia na inną okazję.
opr. jj, źródło: Claas